Toyota production in Japan hit by parts crunch from COVID-19
The shortage of parts caused by the coronavirus pandemic is further denting production at Toyota, Japan’s top automaker
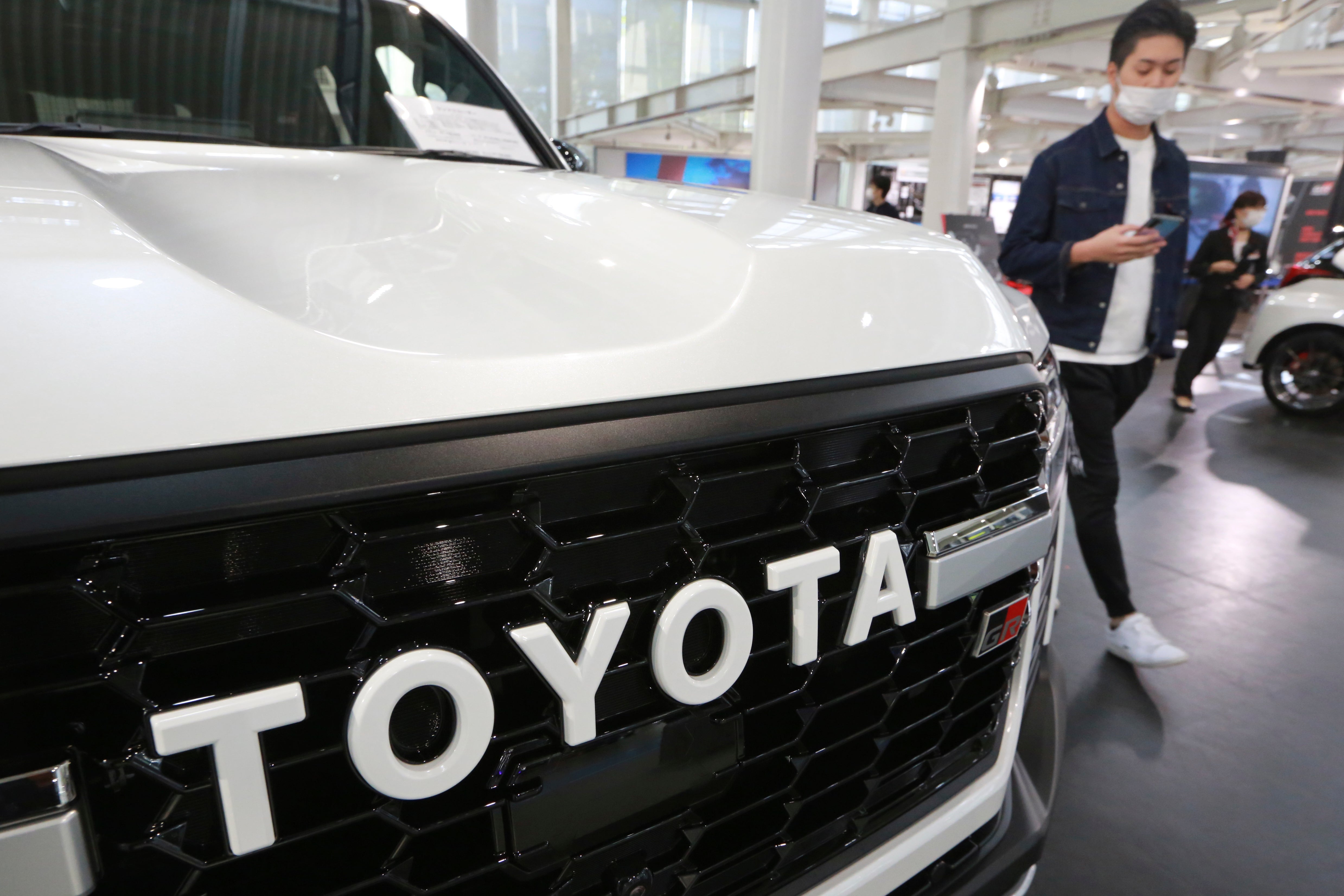
Your support helps us to tell the story
From reproductive rights to climate change to Big Tech, The Independent is on the ground when the story is developing. Whether it's investigating the financials of Elon Musk's pro-Trump PAC or producing our latest documentary, 'The A Word', which shines a light on the American women fighting for reproductive rights, we know how important it is to parse out the facts from the messaging.
At such a critical moment in US history, we need reporters on the ground. Your donation allows us to keep sending journalists to speak to both sides of the story.
The Independent is trusted by Americans across the entire political spectrum. And unlike many other quality news outlets, we choose not to lock Americans out of our reporting and analysis with paywalls. We believe quality journalism should be available to everyone, paid for by those who can afford it.
Your support makes all the difference.The shortage of parts caused by the coronavirus pandemic is further denting production at Toyota Japan’s top automaker.
Production at 11 plants in Japan will be halted Friday, Saturday and next Monday, Toyota Motor Corp. said.
That comes on top of reductions planned for February that were announced earlier. Those reduction will be on various days at eight of its 14 plants in Japan, including assembly lines making the Prius hybrid and Lexus luxury models.
Supplies are running short because of a lack of computer chips, which are crucial in auto parts. Plants in and out of Japan have undergone lockdowns and stoppages related to COVID-19 measures. Toyota has not given details.
Production in January will be reduced by 47,000 vehicles, when accounting for the latest changes, according to Toyota. For the fiscal year through March, production will now fall short of the 9 million vehicles the automaker had targeted, despite healthy demand for Toyota offerings. All manufacturers are scrambling to secure the tight chips supply, worsening the crunch, Toyota said.
“We are doing our utmost to deliver our vehicles to our customers as soon as possible,” it said in a statement. “We deeply apologize.”
Toyota has periodically released information about COVID-19 among its workers. Toyota said four workers at a line at Tsutsumi plant in Toyota city, Aichi prefecture, became sick, so it was shut down. Earlier in the week, 14 workers tested positive at another line at the same factory, shutting down daytime operations for four days.
The pandemic has disrupted not only the auto sector but various areas, including shipping, the oil supply and meat packing, serving as a reminder of the connectivity of the world and the importance of the humblest worker.
Matteo Fini, vice president, who analyzes auto supply chains and technology for IHS Markit, said supply problems aren’t expected to go away for some time, and they are serious, costing manufacturers as much as $50 million a week.
That means the cost-savings from the famous “Toyota Way” of lean manufacturing, based on having as little inventory as possible for “just-in-time” production, may no longer pay off, said Fini.
“The recent experience of these input shortages is forcing automakers to go against everything they have done in the past 30 years when it comes to supply chain management,” he said.
“Carmakers are now considering taking on inventory for certain parts because, in relative terms, it costs peanuts to have that inventory compared with having a line stoppage.”
___
Yuri Kageyama is on Twitter https://twitter.com/yurikageyama