Scientists accidentally make ‘impossible material’ Upsalite - the world’s most efficient water absorber
Human error solves problem of how to produce world’s most efficient water absorber more cheaply
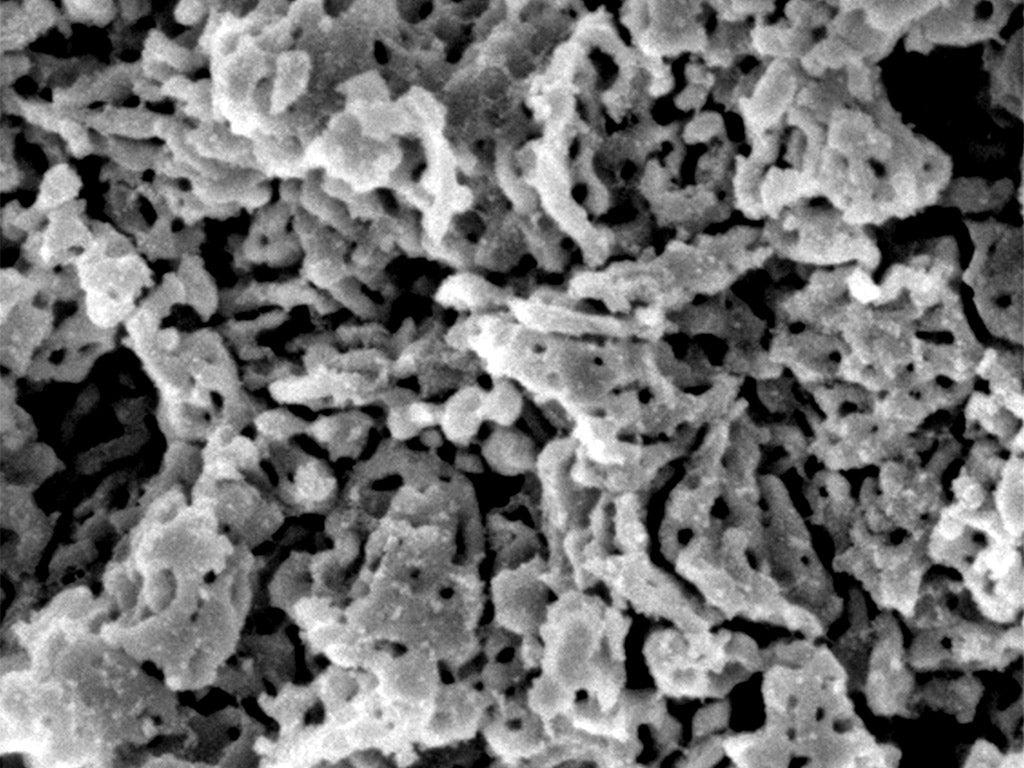
Your support helps us to tell the story
From reproductive rights to climate change to Big Tech, The Independent is on the ground when the story is developing. Whether it's investigating the financials of Elon Musk's pro-Trump PAC or producing our latest documentary, 'The A Word', which shines a light on the American women fighting for reproductive rights, we know how important it is to parse out the facts from the messaging.
At such a critical moment in US history, we need reporters on the ground. Your donation allows us to keep sending journalists to speak to both sides of the story.
The Independent is trusted by Americans across the entire political spectrum. And unlike many other quality news outlets, we choose not to lock Americans out of our reporting and analysis with paywalls. We believe quality journalism should be available to everyone, paid for by those who can afford it.
Your support makes all the difference.It is so difficult to make that the researchers who first discovered it called it the “impossible material”.
Now a century later, a team of Swedish scientists have done the impossible by producing the substance known as Upsalite by accident – after leaving their equipment running over the weekend.
The breakthrough has far-reaching commercial applications, as Upsalite (named after the University of Uppsala, where the scientists are based) is the world’s most efficient water absorber, with potential to be used for the removal of moisture in drug creation and high-tech electronics to cleaning up huge oil spills.
A single gram of this elusive white, dry, powdered form of magnesium carbonate (MgCO3) has an extraordinarily-large surface area of 800 square meters thanks to numerous minuscule pores, each one a million times smaller than the width of a human hair.
“Upsalite absorbs more water and low relative humidities than the best materials presently available and can be regenerated with less energy consumption than is used in similar processes today,” said Maria Stromme, professor of nanotechnology at Uppsala University.
“This, together with other unique properties of the discovered impossible material, is expected to pave the way for new sustainable products in a number of industrial applications,” she said.
Other uses include ice hockey rinks, warehouses, the collection of toxic waste or chemical spills and odour control.
MgCO3 is also about as dry as a material can get, a property which, combined with a huge relative surface area that is inundated with pocket pores, makes it the world’s best mop. The only problem is that, until now, this absorbent form of magnesium carbonate could only be produced by a process that is so expensive and involves so much heat that it wasn’t remotely feasible to use it. While other members of the so-called “disordered carbonates” family could be produced more cheaply and simply – by bubbling carbon dioxide through a mixture containing alcohol – a group of German researchers claimed in 1908 that this method couldn’t be used to make dry MgCO3. And so they dubbed it the “impossible material”.
The irony is that although the Uppsala team had been trying to create the impossible material, they had been going about it the wrong way.
“A Thursday afternoon in 2011, we slightly changed the synthesis parameters of the earlier employed unsuccessful attempts, and by mistake left the material in the reaction chamber over the weekend. Back at work on Monday morning we discovered that a rigid gel had formed and after drying this gel we started to get excited,” says Johan Gomez de la Torre.
The unwitting solution still involved bubbling the Co2 through the alcohol mixture, but at three times normal atmospheric pressure. A year of detailed analysis and experimental fine tuning followed, during which time it was discovered that when heated to 70C the resulting gel solidifies and collapses into a white and coarse powder.
“It became clear that we had indeed synthesised the material that previously had been claimed impossible to make. This places it in the exclusive class of porous, high surface area materials,” said Ms Stromme.
The findings have been published in the journal PLOS ONE.
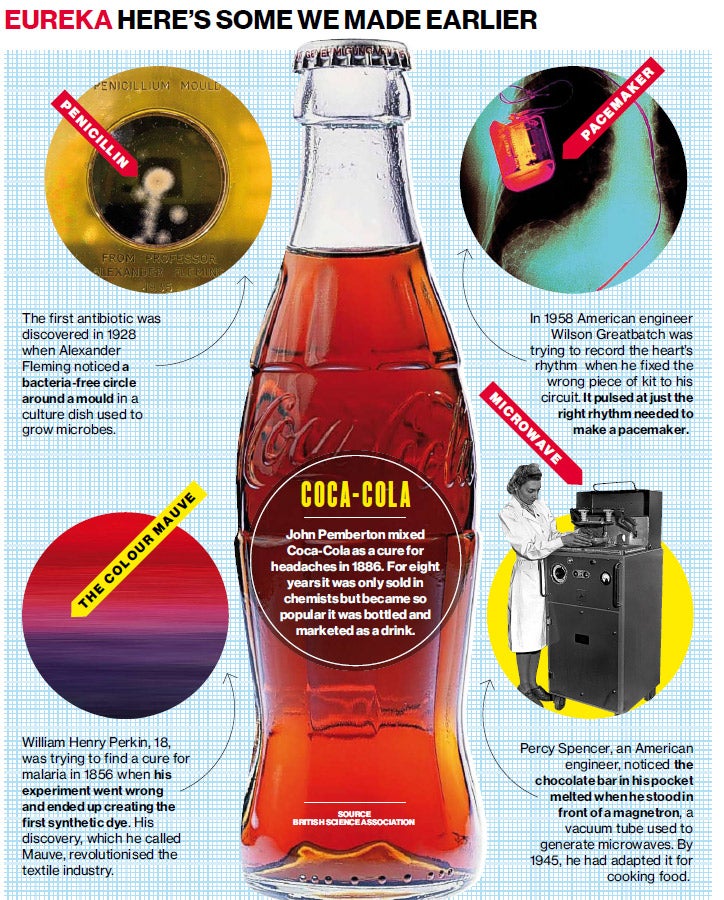
Join our commenting forum
Join thought-provoking conversations, follow other Independent readers and see their replies
Comments