Scientists produce biodegradable plastic made from fish waste
‘When we start the process, there is a faint kind of smell, but that disappears,’ explains Francesca Kerton, lead project investigator
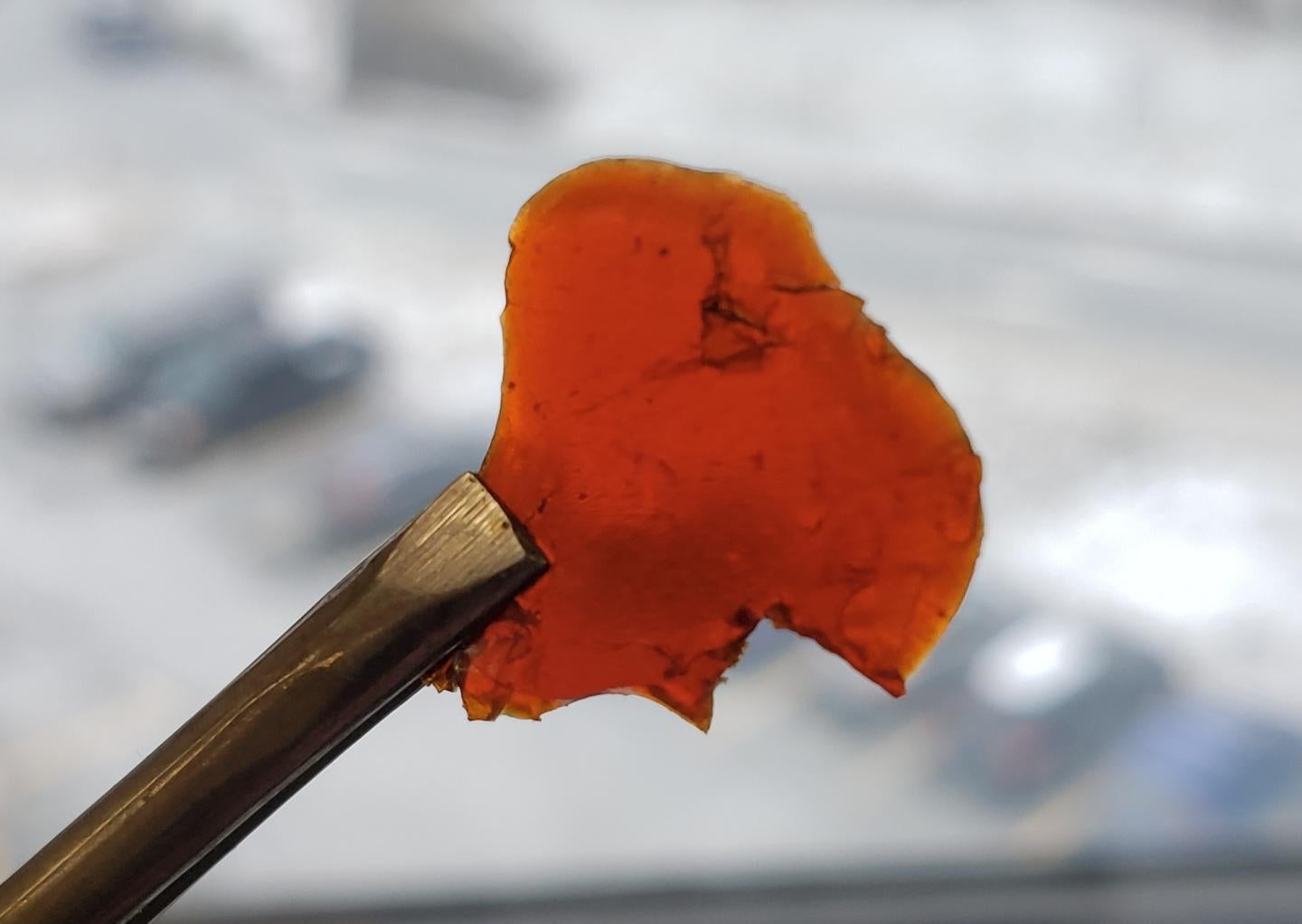
Your support helps us to tell the story
From reproductive rights to climate change to Big Tech, The Independent is on the ground when the story is developing. Whether it's investigating the financials of Elon Musk's pro-Trump PAC or producing our latest documentary, 'The A Word', which shines a light on the American women fighting for reproductive rights, we know how important it is to parse out the facts from the messaging.
At such a critical moment in US history, we need reporters on the ground. Your donation allows us to keep sending journalists to speak to both sides of the story.
The Independent is trusted by Americans across the entire political spectrum. And unlike many other quality news outlets, we choose not to lock Americans out of our reporting and analysis with paywalls. We believe quality journalism should be available to everyone, paid for by those who can afford it.
Your support makes all the difference.Scientists working on an alternative to polluting plastic have discovered a biodegradable material derived from fish waste that would otherwise be thrown away, which could be used in a variety of products including packaging and clothing.
Canadian researchers say fish heads, bones, skin and guts heading for landfill can be turned into useful material that could replace crude oil-derived polyurethanes, which are found in everything from shoes and clothes to refrigerators and construction materials.
Existing polyurethanes come with a large carbon footprint and are slow to break down.
But the team, led by Francesca Kerton, who is based at the Memorial University of Newfoundland, found that fish-oil based plastics could provide an environmentally friendly solution while also tackling food factory waste.
Previous studies have developed methods for producing plastics from fish waste, but the latest research goes further in determining how the material might be easily broken down again at the end of its useful life.
Read more:
- Bitcoin mining is disastrous for the environment – it is time for governments to intervene
- Tiny minorities take most flights in countries with highest air travel emissions, report says
- ‘Cancer-causing’ chemicals found in children living near fracking well sites
- Welcome to Dunbar, Scotland’s first zero-waste town
To produce the new material, the researchers used oil extracted from bits of salmon left after the flesh had been removed and processed for human consumption.
They developed a way of converting the fish oil into a polyurethane-like polymer, first by adding oxygen to the oil in a controlled way to form epoxides, molecules similar to those in epoxy resin.
Then, carbon dioxide was added to the epoxides and the resulting molecules combined with nitrogen-containing chemical compound amines to form the new material.
“It is important that we start designing plastics with an end-of-life plan, whether it's chemical degradation that turns the material into carbon dioxide and water, or recycling and repurposing,” Ms Kerton said.
“When we start the process with the fish oil, there is a faint kind of fish smell, but as we go through the steps, that smell disappears.”
Since last summer, the team has been tweaking that process to simplify and speed up the breakdown of the fish oil-derived plastic.
Experiments suggested the new material might biodegrade readily when required.
In one, pieces of the plastic were soaked in water, some with lipase, an enzyme that breaks down fats in fish oil.
Under a microscope, the researchers saw microbial growth on the samples, including those that had been placed just in plain water. The team said the results offered an encouraging sign that the new material might biodegrade readily.
Ms Kerton and Mikhailey Wheeler, a graduate researcher who has worked on the project, said they intended to study how it might potentially be used in real world applications, such as in packaging or fibers for clothing.
“I find it interesting how we can make something useful, something that could even change the way plastics are made, from the garbage that people just throw out,” said Ms Wheeler, also of Memorial University of Newfoundland.
Polyurethanes are traditionally made using crude oil and phosgene, a toxic gas, and the process generates isocyanates, which are powerful irritants to the eyes and gastrointestinal and respiratory tracts, with links to severe asthma attacks.
In addition, the final product does not readily break down in the environment and the limited biodegradation that does occur can release carcinogenic compounds.
Past research has resulted in polyurethanes made using plant-derived oils to replace petroleum, however the researchers said these were not without their downsides either as the crops, often soybeans, require land and resources.
The research, which was carried out with support from the Natural Sciences and Engineering Research Council of Canada, was due be presented at a meeting of the American Chemical Society (ACS) on Monday.
Join our commenting forum
Join thought-provoking conversations, follow other Independent readers and see their replies
Comments