Smart robots do all the work at Nissan's 'intelligent' plant
Nissan’s “intelligent factory” hardly has any human workers
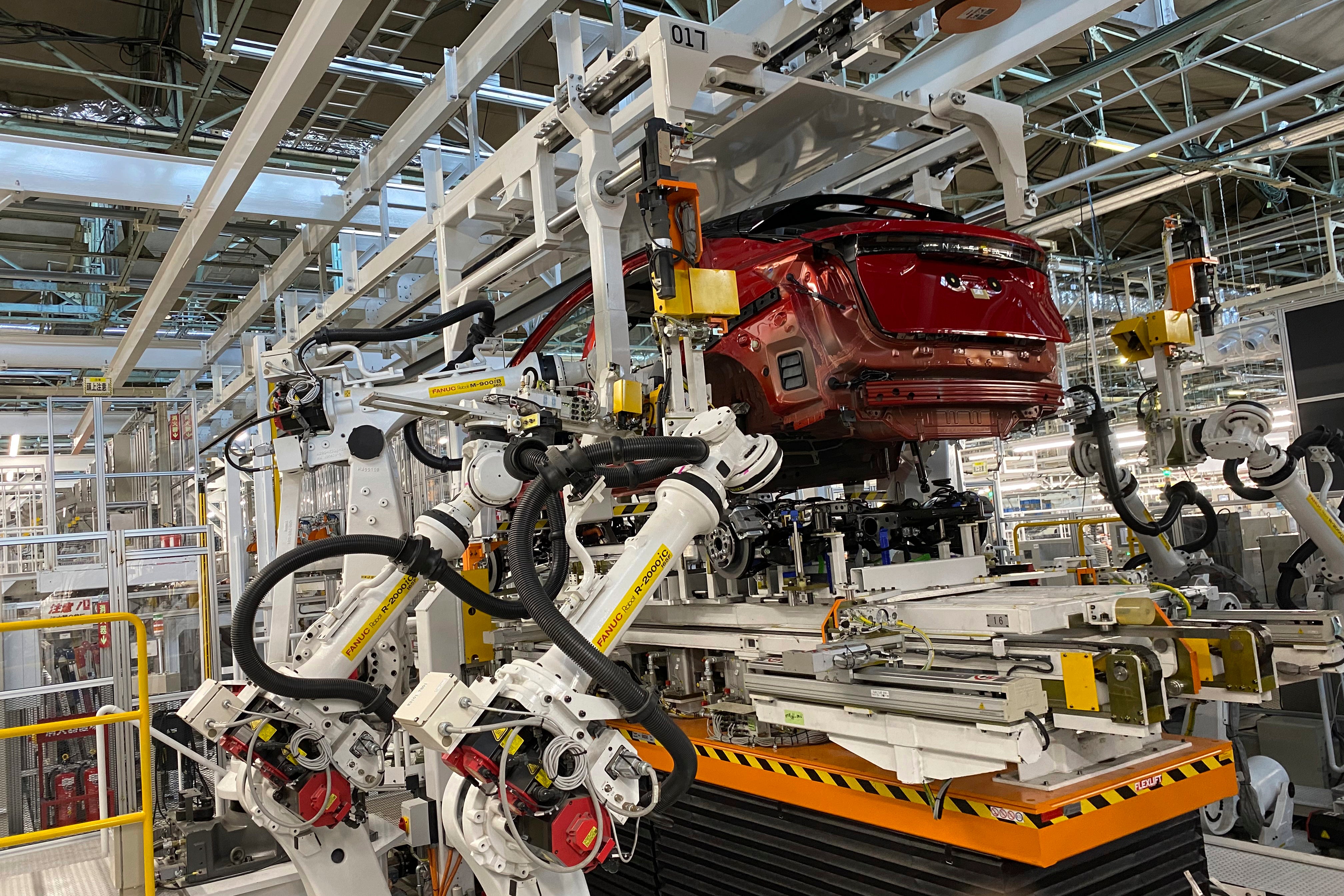
Your support helps us to tell the story
From reproductive rights to climate change to Big Tech, The Independent is on the ground when the story is developing. Whether it's investigating the financials of Elon Musk's pro-Trump PAC or producing our latest documentary, 'The A Word', which shines a light on the American women fighting for reproductive rights, we know how important it is to parse out the facts from the messaging.
At such a critical moment in US history, we need reporters on the ground. Your donation allows us to keep sending journalists to speak to both sides of the story.
The Independent is trusted by Americans across the entire political spectrum. And unlike many other quality news outlets, we choose not to lock Americans out of our reporting and analysis with paywalls. We believe quality journalism should be available to everyone, paid for by those who can afford it.
Your support makes all the difference.Nissan’s “intelligent factory” hardly has any human workers. The robots do the work, including welding and mounting. They do the paint jobs and inspect their own paint jobs.
“Up to now, people had to make production adjustments through experience, but now robots with artificial intelligence, analyzing collected data, are able to do it. The technology has developed to that level,” Nissan Executive Vice President Hideyuki Sakamoto said during a tour of the production line for the Ariya sport-utility vehicle at its Tochigi plant Friday.
The factory, on the outskirts of Tokyo is set to be up and running sometime before April, according to Nissan Motor Co.
Its assembly line is designed so that all three types of models — electric; e-Power, which has both a motor and an engine, and those powered by regular combustion engine — can be built on the same line. Each vehicle is equipped with the right powertrain as it moves along the line.
The workers at the factory can focus on more skilled work such as analyzing data collected by the robots, and on maintaining the equipment.
All automakers are working on robotic technology that can increase adaptability and enable them to respond quickly to market demand.
During the tour, giant mechanical arms equipped with large displays shone light from the displays on to the car’s surfaces from various angles so that cameras could detect the tiniest flaws.
A mechanism quickly wound wires around a metal object that looked like a giant spool, a motor part that Nissan is using to replace magnets now used in electric vehicles. The company says the innovation eliminates the need for rare earth materials, cutting costs.
Nissan said the innovations being tested in Tochigi will be gradually rolled out at its other global plants, including French alliance partner Renault’s factories.
Sakamoto said it was difficult to estimate exactly how much the fully automated assembly line will save.
But he said manufacturing needs to adapt to labor shortages, to the coronavirus pandemic and to lower carbon emissions to help mitigate climate change.
Nissan says that by 2050 it hopes to achieve carbon neutrality across its operations and the life cycle of its products, which includes raw material extraction, manufacturing, use and recycling.
A new kind of paint that enables vehicles’ bodies and bumpers to be simultaneously painted and baked reduces energy consumption by 25%, the company says.
Before, vehicle bodies, which are aluminum, and plastic bumpers had to be painted separately at different temperatures.
Nissan is expecting to regain profitability in this fiscal year, but like other automakers, it is contending with parts shortages caused by the pandemic. Its brand took a hit from a scandal centered on its former chairman, Carlos Ghosn who was arrested in Japan on financial misconduct charges in 2018.
___
Yuri Kageyama is on Twitter https://twitter.com/yurikageyama