Why are UK shoppers facing shortages of home and garden items?
Camping equipment and garden furniture are the latest items to be in short supply - but what is causing the problems and when might they end? Ben Chapman investigates
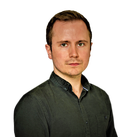
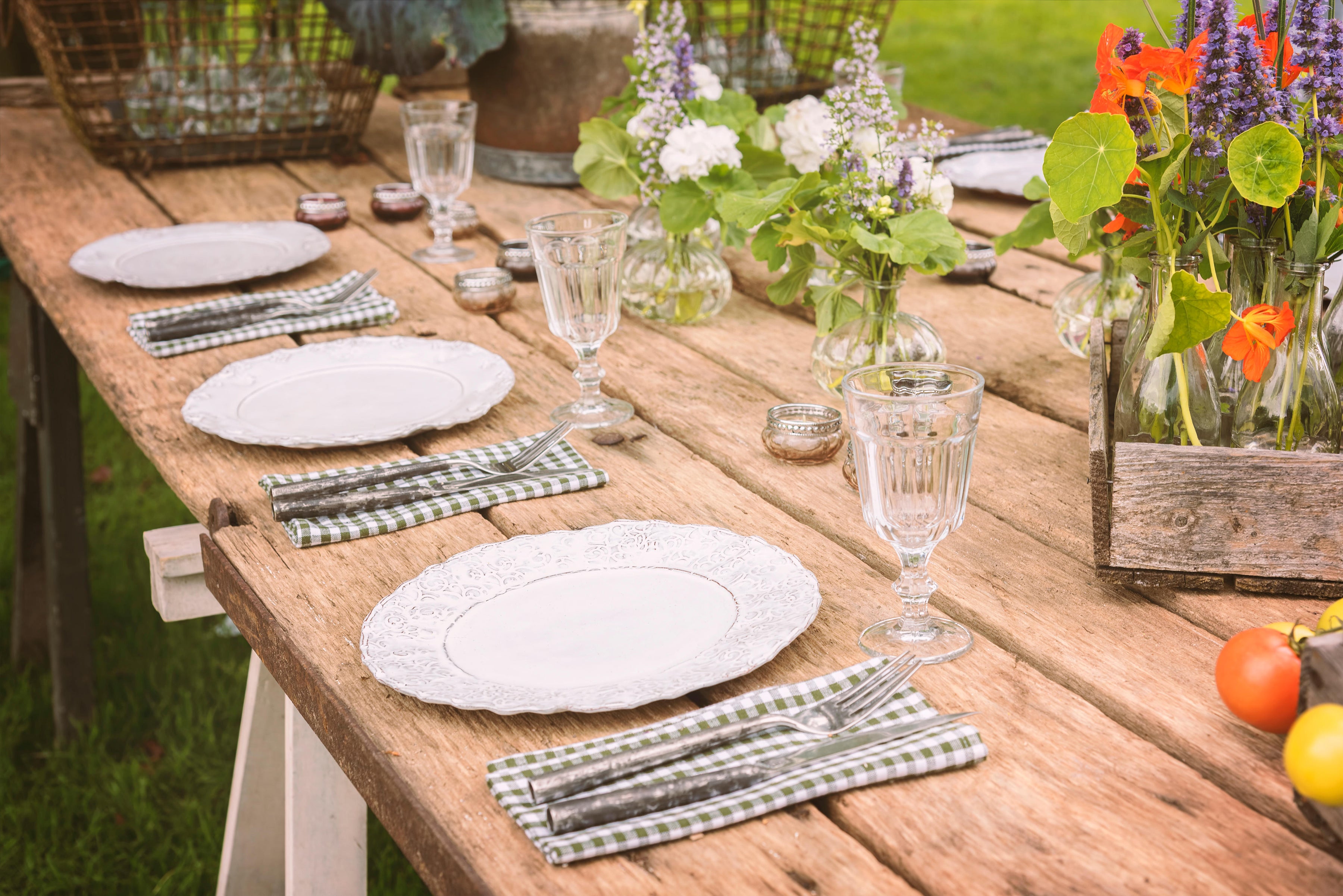
Your support helps us to tell the story
From reproductive rights to climate change to Big Tech, The Independent is on the ground when the story is developing. Whether it's investigating the financials of Elon Musk's pro-Trump PAC or producing our latest documentary, 'The A Word', which shines a light on the American women fighting for reproductive rights, we know how important it is to parse out the facts from the messaging.
At such a critical moment in US history, we need reporters on the ground. Your donation allows us to keep sending journalists to speak to both sides of the story.
The Independent is trusted by Americans across the entire political spectrum. And unlike many other quality news outlets, we choose not to lock Americans out of our reporting and analysis with paywalls. We believe quality journalism should be available to everyone, paid for by those who can afford it.
Your support makes all the difference.Shoppers are facing shortages of goods this summer as the economy opens up rapidly and households begin to spend money they have saved during the pandemic while businesses face a host of problems importing goods.
Items in high demand such as garden furniture, picnic baskets and camping equipment are among those that experts are forecasting will be in short supply.
But why exactly are retailers having such difficulty and what might it mean for ordinary households?
The first and most obvious set of issues stem from the pandemic.
Many manufactured goods produced in China and elsewhere in Asia are experiencing delays in shipping. Global demand for goods dropped at an an unprecedentedly rapid rate last year as much of the world went into lockdown.
This year, it has risen almost as sharply and manufacturers have struggled to increase supply quickly enough resulting in bottlenecks in international supply chains.
Computer chips and construction materials were among the first to see rapid price rises with shortages expected to continue into next year. Some large buyers began to stockpile vital parts in anticipation of future shortages, further exacerbating problems.
These shortages in turn have begun to filter through to consumer goods, with builders’ merchants and DIY stores putting up prices of timber and electronics firms unable to keep up with huge demand. Sony’s PS5 has been in and out of stock all year with buyers snapping up each batch of the popular games console within minutes.
Many have gone on to be swiftly re-sold at hefty mark-ups on eBay, Gumtree and elsewhere. In online forums and on messaging apps like Discord, traders are making small fortunes buying and selling graphics cards, consoles and other items in high demand and short supply.
Shipping routes have been slowed by Covid safety measures at ports and a backlog caused by the blockage of the Suez Canal earlier in the year. Competition for space in the shipping containers that transport much of the world’s produce is fierce and prices have surged.
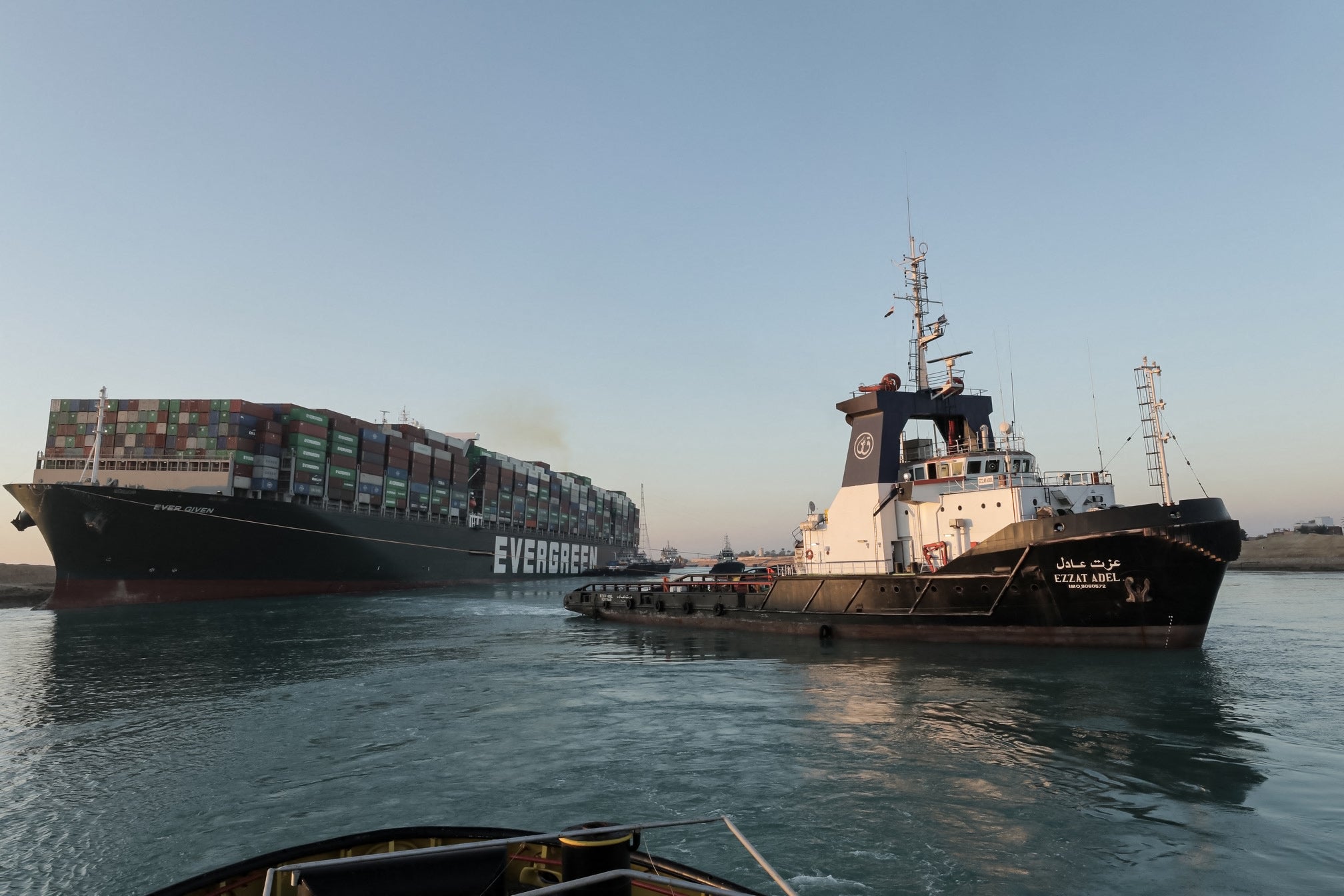
Adding to this combination of challenges is Brexit which has left businesses with a significant extra burden of paperwork this year. Problems are set to get worse as full customs controls are phased in over coming months.
Darran Major, a plant buyer for a large independent garden centre in Hertfordshire, said growers, hauliers and everyone else in the supply chain has worked tirelessly to ensure a smooth transition.
“Pre-Brexit, plant imports from the EU were very straightforward as we all seemed to ‘sing from the same song sheet’,” he said.
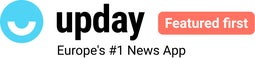
Now, businesses must deal with much more administrative work for every shipment.
“Plant passports and phytosanitary certificates need to be issued for every plant. This has obviously had huge implications on costs and turn-around times of orders.”
“The only issue really is the additional paperwork. This is now unavoidable and although it may help towards ensuring only healthy and sustainable plants are entering the UK, it is an additional cost implication, which will ultimately be handed down to the end user.”
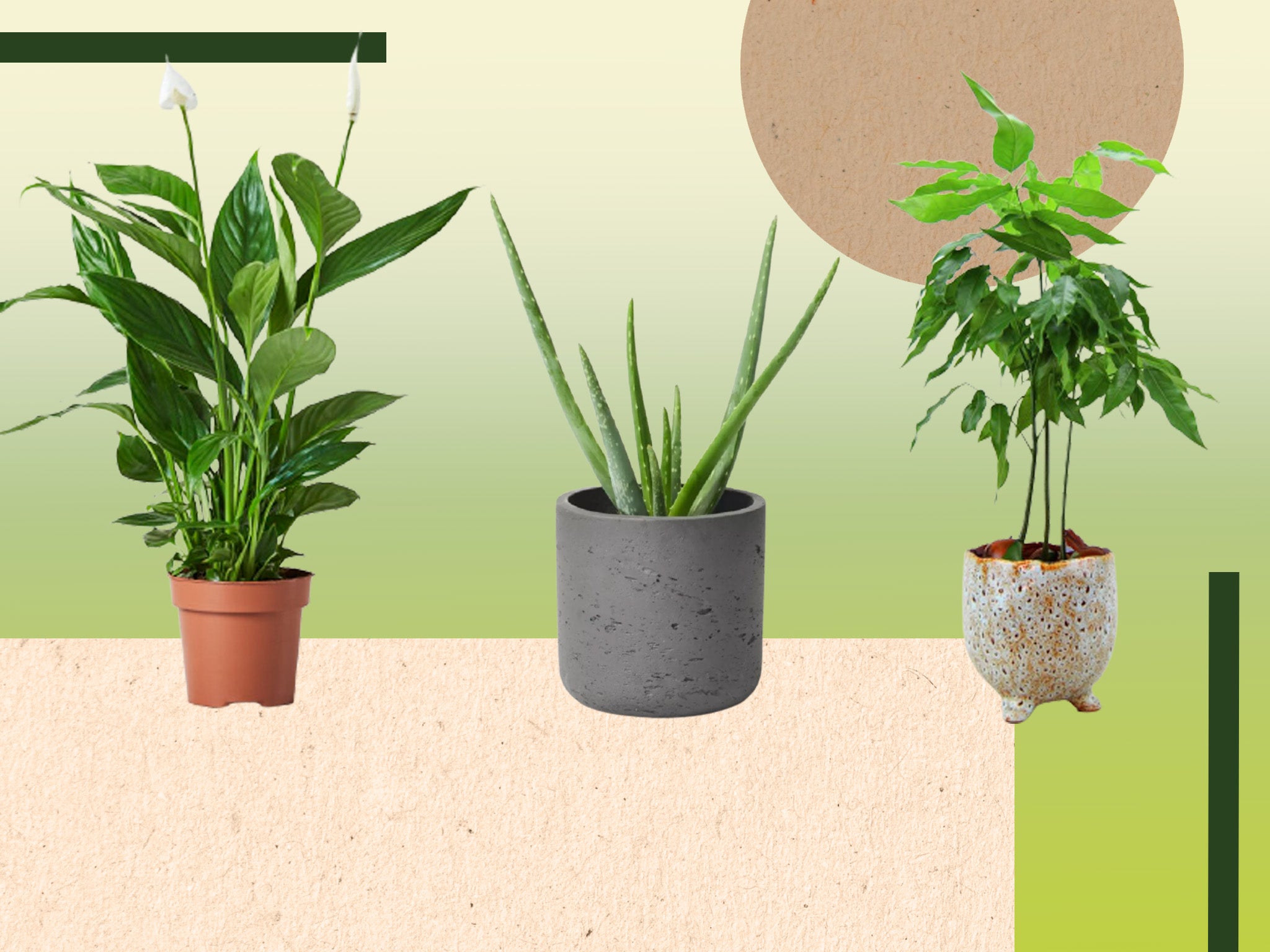
A poll by Haulage Exchange, a company that provides technology for the logistics industry, found that 94 per cent of UK hauliers have been negatively impacted by Brexit. More than two-thirds of UK haulage companies have lost business while 31 per cent said they might stop working with food and drinks clients due to rule changes since the UK left the EU.
A separate survey by customs clearance platform KlearNow indicated that about 60 per cent of British suppliers have experienced import delays in the past month.
"With competition for container space so high, some smaller businesses are simply being priced out of landing the goods and materials that they need," said Sam Tyagi, chief executive of KlearNow.
"We’ve processed more than a 100,000 UK customs documents since January and speak to many UK businesses every day. The one word we keep hearing is chaos. UK businesses are facing an increasing array of supply chain challenges already and it’s only going to get worse."
For shoppers, this means higher prices of many items are likely to be a fixture for some time. Consumers have begun turning increasingly to rental sites and secondhand platforms.
Online retailer Shpock has seen a 157 per cent increase in home and garden sales in the second quarter of the year.
Iyesha Cheema-Bradshaw, brand manager at Shpock, said short supply of home and garden essentials meant it was the ideal time to turn to second-hand platforms.
“We’ve noticed a sharp increase in garden sales as buyers look towards platforms with a plentiful supply of quality items,” she said.
While many of the current problems are transitory and are expected to subside as the virus is brought under control, others are built into the system and may need to be reconsidered in a post-Covid world.
For decades, companies have embraced “Just In Time” methods, holding only a the smallest number of parts and stock needed so they can save on storage and other costs.
While the approach allows them to be nimble, it also means far less ability to absorb unforeseen shocks, adding significant amount of fragility to the system.
Less inventory means shortages have a greater impact more quickly and prices more prone to spiking when something in the supply chain goes wrong.
Will it change after Covid? Arguably, there will be some impetus to build greater resilience into the system.
But companies’ incentives remain skewed towards short-term returns for shareholders. Chief executives are rewarded handsomely for boosting the share price and handing out dividends; there are far fewer financial rewards on offer for building long-term resilience and spare capacity.
Join our commenting forum
Join thought-provoking conversations, follow other Independent readers and see their replies
Comments