UK wastes billions as scrap is sent abroad
Lack of adequate recycling facilities and confusing legislation is hampering Britain's economy as demand for raw materials soars. Tom Bawden examines the case
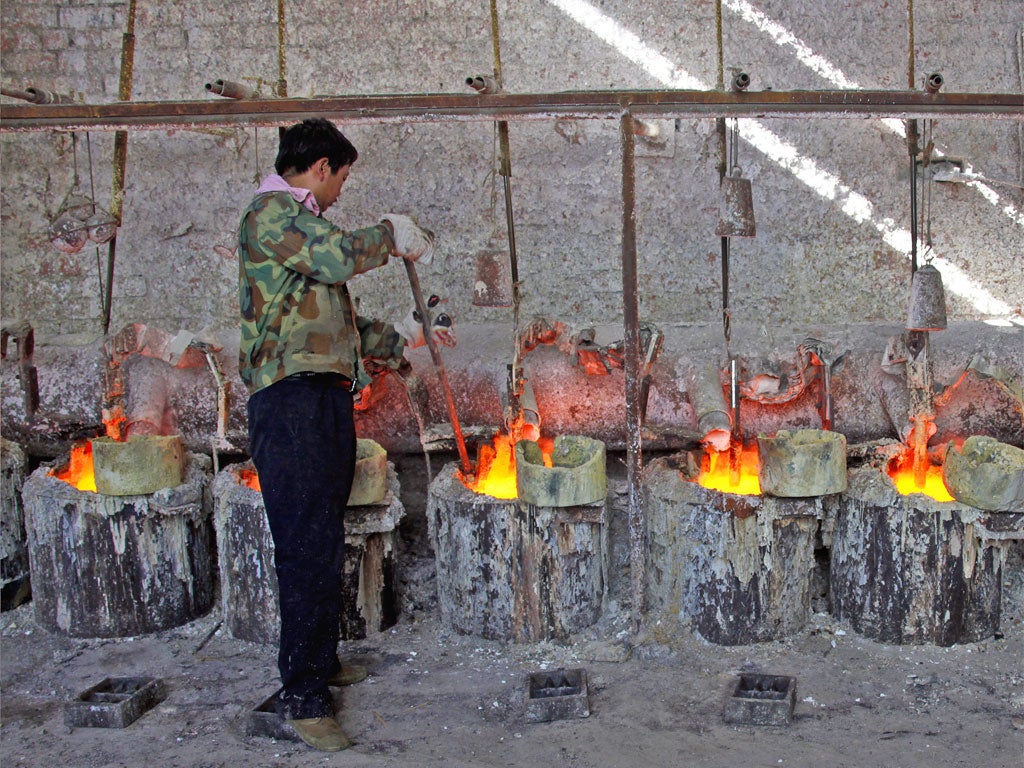
Your support helps us to tell the story
From reproductive rights to climate change to Big Tech, The Independent is on the ground when the story is developing. Whether it's investigating the financials of Elon Musk's pro-Trump PAC or producing our latest documentary, 'The A Word', which shines a light on the American women fighting for reproductive rights, we know how important it is to parse out the facts from the messaging.
At such a critical moment in US history, we need reporters on the ground. Your donation allows us to keep sending journalists to speak to both sides of the story.
The Independent is trusted by Americans across the entire political spectrum. And unlike many other quality news outlets, we choose not to lock Americans out of our reporting and analysis with paywalls. We believe quality journalism should be available to everyone, paid for by those who can afford it.
Your support makes all the difference.Companies are flushing millions of tonnes of valuable raw materials down the drain, a significant drag on the economy at a time of high commodity prices and a looming shortage of key industrial metals and minerals, according to a damning report.
Britain exports 15 million tonnes of industrial waste each year, half of which is valuable scrap metal, because it does not have sufficient recycling facilities and clear enough legislation to deal with it here, according to the report, by manufacturers' organisation EEF.
Britain's recycling infrastructure is so poor that industrial waste by weight makes up one sixth of our total exports.
The EEF's report comes against a backdrop of unprecedented strain on the world's resources, which has pushed prices up considerably in the past two years and made them farmore volatile.
The price of europium oxide, a so-called rare earth metal with phosphorescent properties used in energy-saving lightbulbs, plasma TVs and smartphones, has seen a sevenfold rise in price in the past two years.
Meanwhile, the price of dysprosium oxide, a key additive used in magnets found in computer hard drives and wind turbines, has jumped by a factor of five in the past year.
The prices of the 17 rare earth metals have soared in the past two years as China, which produces 97 per cent of the global supply, seeks to keep more of them for itself.
And while the price of key commodities may have declined from record highs in the last few months of 2011, they are back on the rise with copper, nickel, tin, lead and zinc all up by more than 10 per cent so far this year.
The squeeze on resources will intensify as electronic goods proliferate to meet the demands of the growing number of more affluent consumers worldwide, who are set to increase from 1.8 billion to nearly 5 billion by 2030. Malcolm Preston, the global head of sustainability at PwC, said: "Everybody has suddenly realised that the scarcity of raw materials was much worse than they thought. In five years' time, it's going to be a really big issue."
Carmakers, chemical producers and energy generators are most at risk from the growing shortage of metals and minerals, Mr Preston said.
The EEF survey of 200 leading manufacturing executives showed that two-thirds see raw materials shortages as the biggest threat to their businesses, ahead of even the eurozone crisis.
Manufacturers are calling on the Government to act decisively by fostering a new generation of specialised, affordable and accessible recycling centres.
Furthermore, 20-year old legislation dictating how British companies deal with their waste is "unnecessarily complex, confusing and based on out-of-date assumptions" and must be overhauled, the EEF said.
The report notes that Britain's waste legislation still assumes it will be sent direct to landfill, even though less than a quarter of manufacturing waste is disposed this way".
The problem is compounded in the UK, where many component-makers have closed in recent years, making manufacturers reliant on imports and vulnerable to supply-chain shocks, such as the Japanese earthquake and tsunami last year.
The Department for Environment, Food and Rural Affairs (Defra) recognised in September that "the issue of security of resources is of increasing concern for UK businesses and the economy".
It noted that, although raw materials were unlikely to run out in the near future, there were fears about "interruptions to supply and associated price volatility from, for example, increasing demand, local regulatory action or geo-political issues."
Defra is preparing to publish a report next month on how to address potential raw material shortages. This will explore how to improve recovery, recycling and re-use of critical resources and what further research needs to be done in the area.
However, Susanne Baker, a senior policy adviser on climate and the environment at the EEF, said Defra's actions, while welcome, do not go far enough.
"It's only embryonic, it is not ambitious enough and doesn't go far enough. It's quite narrow in focus and we want a much broader-ranging resources review. The Government has to take more concrete action."
Case study: Henry vacuum cleaners...'Raw materials have emigrated ... we are more and more vulnerable'
Andrew Smith, senior manager at Numatic International
Numatic International has had a "few near misses" of late, only just sourcing the raw materials needed to make its Henry range of vacuum cleaners in time after hiccups in the supply chain.
Andrew Smith, a senior manager at the Chard, Somerset-based cleaning equipment maker, said components have become increasingly difficult to come by in the past 15 years as the demise of British manufacturing and the rise of emerging markets such as China forced suppliers East.
"Raw materials have emigrated, so we are more vulnerable to disruption and have to order further in advance. Fifteen years ago, the majority of our plastics granules came from the UK, but now they mainly come from Europe, with very little from the UK," said Mr Smith, who was head of manufacturing for 20 years before recently taking on a part-time senior management role.
"We've had a few near misses and panics, including one involving a tool breakage at an injection mouldings factory in the Far East, which thankfully we managed to get round by air freighting materials, although at enormous expense.
"I think we just have to accept that we are more and more vulnerable," Mr Smith said.
Mr Smith refused to be drawn on whether it's only a matter of time before raw material shortages hold up production at Numatic, preferring to reiterate that "we've come very close". Reading between the lines, there is certainly a strong possibility. Tom Bawden
Join our commenting forum
Join thought-provoking conversations, follow other Independent readers and see their replies
Comments