Apple reveals latest supply chain responsibility report, revealing new details about how iPhones and other products are actually made
Apple's flagship product is now made without any waste going to landfill at all, saving thousands of football pitches' worth of rubbish going into the ground
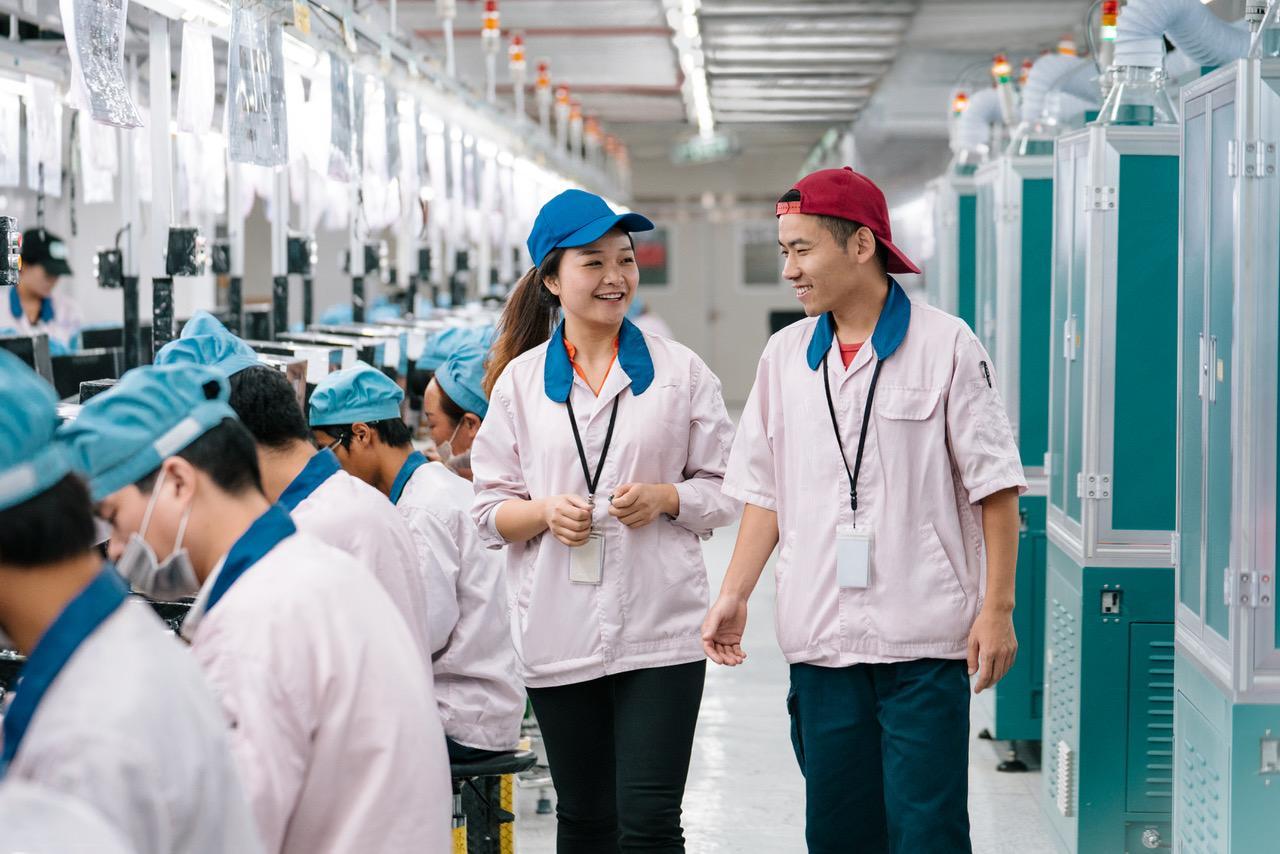
Your support helps us to tell the story
From reproductive rights to climate change to Big Tech, The Independent is on the ground when the story is developing. Whether it's investigating the financials of Elon Musk's pro-Trump PAC or producing our latest documentary, 'The A Word', which shines a light on the American women fighting for reproductive rights, we know how important it is to parse out the facts from the messaging.
At such a critical moment in US history, we need reporters on the ground. Your donation allows us to keep sending journalists to speak to both sides of the story.
The Independent is trusted by Americans across the entire political spectrum. And unlike many other quality news outlets, we choose not to lock Americans out of our reporting and analysis with paywalls. We believe quality journalism should be available to everyone, paid for by those who can afford it.
Your support makes all the difference.Apple has revealed new details about how exactly the iPhone is made – and how it is trying to improve the lives of people who are actually putting it together.
The new Supplier Responsibility report for 2017 shows just how challenging that is. But it reveals how Apple is continually asking more of itself, and the progress it has made in fixing those issues.
The problem facing Apple and other technology companies is easy to explain, but incredibly difficult and complicated to solve. Those companies are mostly sincere in their desire to ensure the people making the phones in our pockets and the computers on our desks have the best lives they can, and they are largely held responsible when they fail to do so – but the suppliers are sometimes operating separately from companremoved fromies like Apple and often in places with fewer worker protections and more abuses.
The latest report shows Apple making significant progress on a number of the benchmarks it uses to measure its supply chain. And it also sees it introduce some new and profound measures, too: including efforts to educate those who work for its suppliers in their rights, about their health and to work towards progressing them through to more senior positions.
In short, Apple’s report splits its work on supply chain responsibility into three main parts: its people, the planet, and audits that ensure that its suppliers are keeping to what it asks of them. Together, those broadly encompass the substantial work Apple is doing to act within the requirements and responsibilities it has set for itself.
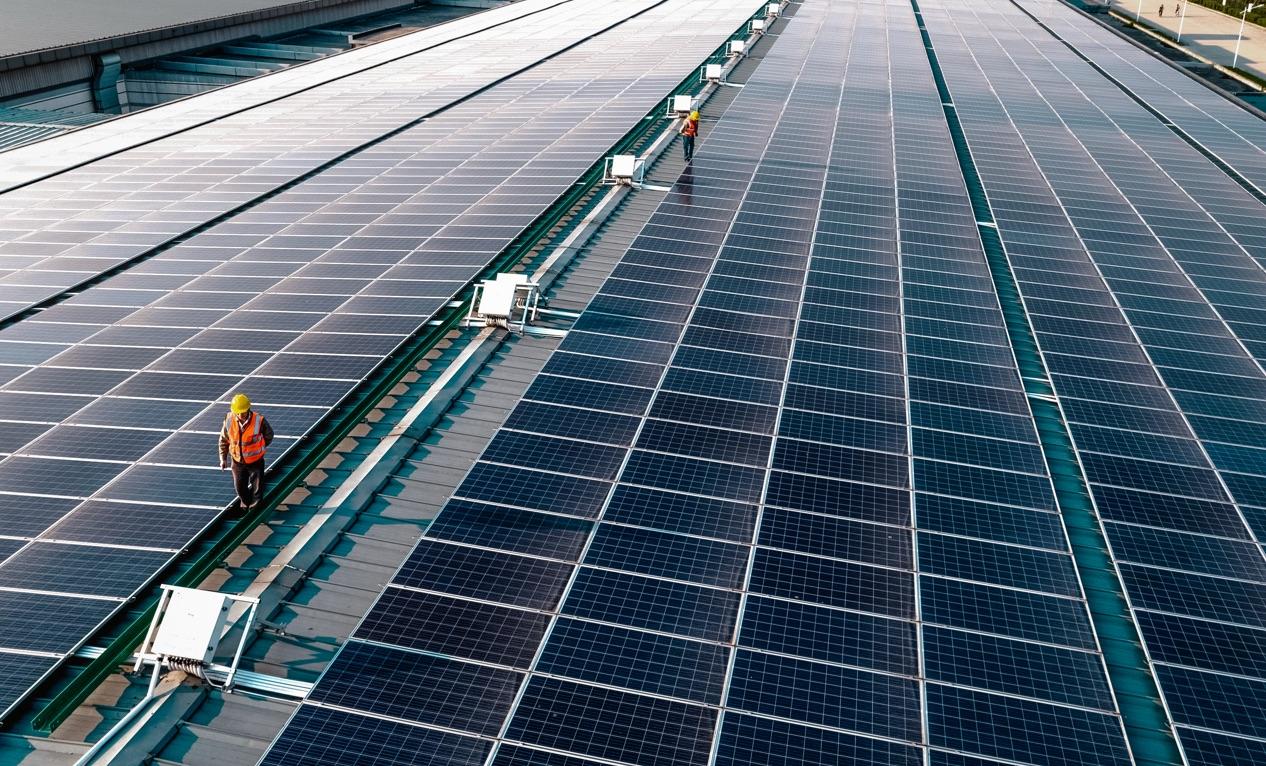
This year, it has worked particularly to focus on the first part of that set – on the people who create its products. It has rolled out new educational programmes aimed at improving the health and wellbeing of the employees who work for its suppliers, and is trying to make sure the benefits from those programmes ripple out far beyond the factory itself, and into the families and communities of those who are involved.
“We believe that everyone making Apple products deserves to be treated with dignity and respect and we’re proud that almost 15 million people understand their workplace rights as a result of the work we’ve done over the years,” said Jeff Williams, Apple’s COO. “ We’re going further with health education programmes and new opportunities for advancement at our suppliers.
“A new preventive health care curriculum is encouraging women to focus on their personal health, and hopefully share that knowledge with their families and communities, Our goal is to reach one million women by 2020. We know our work is never done and we’re committed to raising the bar every year across our supply chain.”
Much of the focus is on the people who make Apple products like the iPhone and iPad. But the report looks at the materials used in those products and their impact on the planet, too.
Those include, for instance, the iPhone – probably the most popular product ever created. With that popularity has become much deserved scrutiny for how the phone itself is made, scrutiny that has moved to other Apple products too.
And Apple is making important breakthroughs in that respect. So with the iPhone, for instance, 100% of final assembly facilities now send zero waste at all to landfill – all of the materials that are thrown off while creating the phone are sent to be re-used or recycled.
Getting to zero waste isn’t just a matter of Apple’s suppliers and their factories – just as important is what happens to things once they’re disposed of and leave the building. So even fixing that is about local communities and education: Apple needs to make sure that once a material leaves the factory, it is being recycled or re-used so that it doesn’t just end up in landfill. That can only be done if the proper recycling facilities are available.
Cutting out waste from the production of iPhones doesn’t just mean cutting down on the materials wasted while they’re being put into the phone. It also means stopping the waste of things used to actually build it, for instance.
So, as an example, there are a host of protective films and liners that sit on the display and ensure it doesn’t get damaged while it is moving through the production process. Before, those were being discarded once the process was over. But now, suppliers are able to take that lining piece, send it to be recycled, and it is turned back into the trays the phone sits in as it’s built, in a neat and circular fix that ensures not only that things aren’t thrown away, but also that they’re staying in the process after they’ve been finished with.
While the iPhone is by far Apple’s biggest product, and therefore the one in which the zero waste programme can have the most impact, that work still isn’t over. Apple acknowledges in its report that “when we waste nothing, that will truly be something”, and it still has a range of products that do lead to waste being put into landfill. But it is increasing, and the amount of waste is shrinking – all of the facilities that do the final assembly of its products are signed up, and the number those making commodities for them increased by 136 per cent from 2016.
The sheer number of Apple products coming out of its supply chain every day is almost too huge to understand; that also means that the potential waste and pollution that is produced is on an equally grand scale. So, for instance Apple’s effort to convert its facilities to renewable energy has cut out as many emissions as would be saved if all the cars in Hong Kong were taken off the road for two months. The zero waste programme that has so cleaned up the production of the iPhones cleared out enough waste that if it were laid a metre deep it would take up more than 2,500 football pitches.
While it is obvious, if not necessarily easy, to measure the impact of plans to cut waste out of the supply chain or how many conflict minerals are used in it, the effect of education can be far more diffuse. Apple is, by design, creating an education programme that will spread out into the community of people around those who create its products – people at many degrees of separation from Apple and even from the people working for its suppliers.
As such, it undertakes conversations with the employees of its suppliers, inside and outside of the facilities. By conducting those conversations, it can measure the impact that the programmes are making – watching over time as they develop, and tweaking things as they do. If Apple encourages one supplier facility to find a way of running on renewable energy, for instance, those discoveries then move across the rest of the supply chain.
That was done in advance of the introduction of the education programmes, too. Among other things, speaking to people in communities ensure that the work is focused on where it is needed: there are significant differences between the health challenges in India and China, for instance, and while one area might have a substantial problem with smoking, others might be helped by efforts to improve gum health.
Just as with the rest of the work across the supply chain, the knowledge gained from those discussions and the practical application of it is then shared with other suppliers. Apple hopes, for instance, that its success in cutting out waste from the production of the iPhone will be able to spread to other supplier facilities and other products like the iPad or the Mac; in exactly the same way, the lessons learned in how best to educate people working at suppliers will spread across the world and between companies.
Apple’s efforts to protect the planet and its people are newer than its work to audit the materials and suppliers used to create its products. But it continues to make strides in that respect, too, the report makes clear: despite the fact that it increases the requirements it asks of suppliers every year, more facilities than ever before managed to satisfy more of them in 2017.
There is, of course, much more to do. Apple will keep increasing its targets, and keep striving to meet them. And it won’t be doing that alone: the various companies that rely on the kinds of huge, complex and often damaging supply chains that are required to produce the products in our pockets are also moving towards a growing recognition of the importance of this work.
Some other companies are still not responding to the challenges in the same way that Apple and other firms at the top of the league tables continue to, either. Electric car manufacturers, for instance, still need to make huge batteries to power their vehicles – and they often do so using cobalt that has been mined in ways that indirectly supports and continues conflict, and potentially without their customers knowing.
Join our commenting forum
Join thought-provoking conversations, follow other Independent readers and see their replies
Comments