Makers HQ: the sampling studio bringing textile manufacturing back to Plymouth
The studio opened its doors in 2018 on the site of an old Jaeger factory. Hazel Sheffield reports
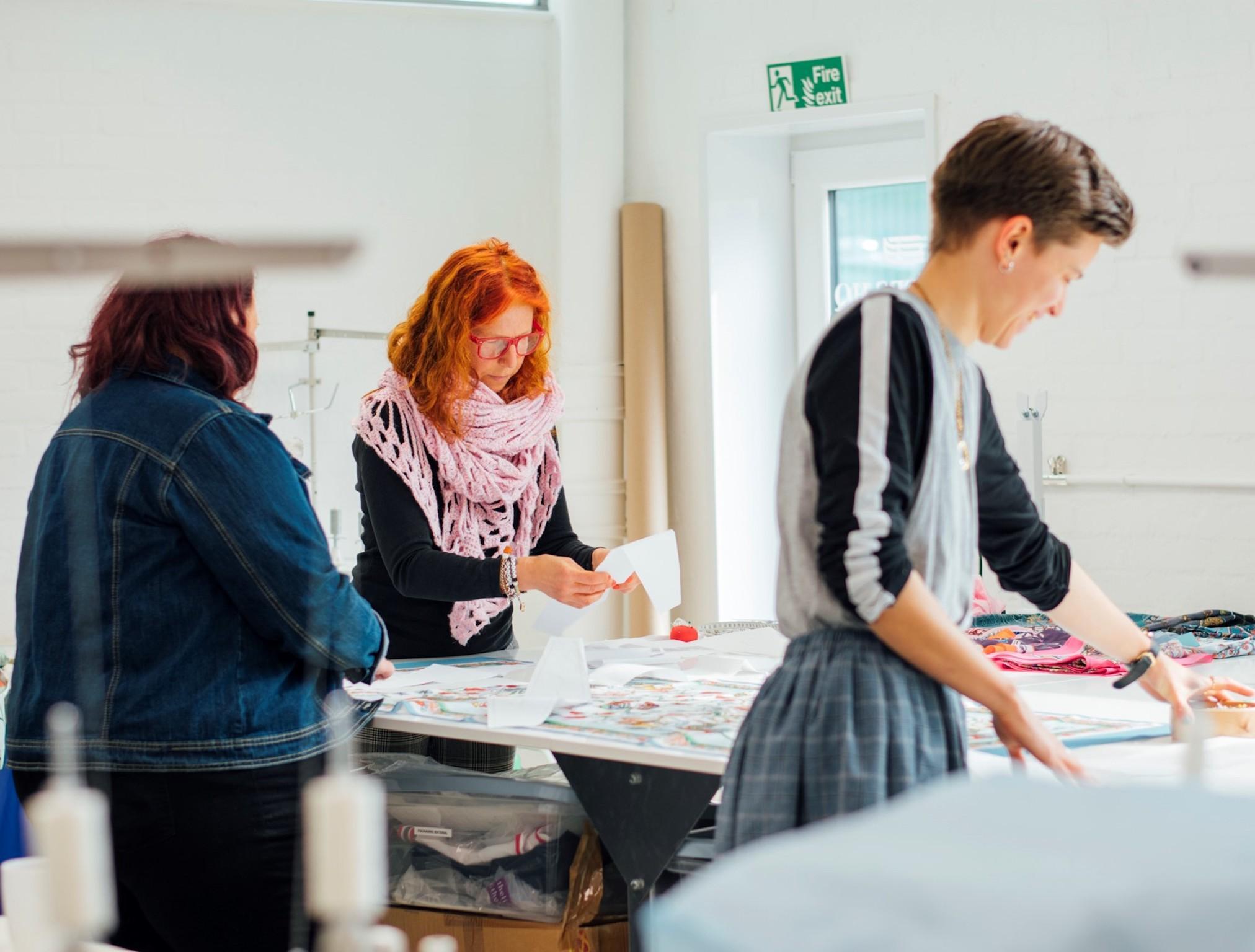
Donna Howell first heard about Makers HQ, a textiles manufacturing studio in Plymouth, when she was looking for somewhere to get a pattern printed. Howell had given up her job supporting students with additional needs to be a stay-at-home mum to her two sons. By last year, the boys were aged six and nine and Howell was wondering what she could do with the rest of her life. She had a degree in fine art, but she wanted to be able to make things. When she saw that Makers HQ offered training courses for people in her position, she immediately applied.
“It’s completely turned my life around,” Howell says, not long after completing the eight-week course, where she learnt how to construct a garment and sew on a machine. The training, which is accredited by ABC Awards, is offered free to people who are unemployed or inactive with funding from the European Social Fund, which supports employment in EU member states.
Howell is now setting up her own business, Dongarees, making dungarees from a home studio. “Makers HQ have helped me with information about how to start it,” she says. “It’s been a whole new learning curve for me. I’m excited and ready to roll.”
Makers HQ opened its doors in August 2018 on the site of the old Jaeger factory on Union Street, which cuts across Plymouth, connecting the city centre to the ferries at Devonport through Stonehouse, one of the city’s most deprived wards. The idea for Makers HQ came from a conversation between Roger Pipe, the chief executive of the Millfields Trust, and Andrew Brewerton, the principal of Plymouth College of Art, in which Brewerton lamented that the college was producing talented graduates but losing many of them to London after graduation.
As chief executive of Millfields Trust, Pipe oversees a charity that was set up to manage the regeneration of Stonehouse, including renting commercial space in the neighbourhood. Pipe said that he would love to hear the whir of sewing machines return to the old Jaeger factory, which closed in 1998 in the face of price competition from overseas, with the loss of 250 jobs.
The two men came up with a plan to consult with old Jaeger employees and academics on a key question: could the south west support the textile industry again?
“Overwhelmingly, the response was yes,” says Sophie Glover, studio manager at Makers HQ, one sunny afternoon in March. By this time, the UK had already voted to leave the EU. Some voters were optimistic that the decision could herald a return to manufacturing in the UK, if the country came to rely less on imports.
There was a major problem: when the UK scrapped its factories, it turned its back on the skilled trades like the pattern cutters and sewing machinists that filled the old factories. “Roger and Andrew wanted to make a business plan that reached some of the longer term unemployed in Stonehouse – the people who are creative but don’t have qualifications – and they had one answer: teach them to sew.”
Over Glover’s shoulder, a group of nine-year-olds in school uniform queue for the sewing machine, clutching sports bibs cut out of red cotton. Jade Rogers, a former Plymouth College student who joined Makers HQ in the summer, operates the machine at the front of the line, showing the children how it makes a running stitch to fix the two parts together.
The school visit is part of an engagement programme run by the Millfields Trust to teach the children about textiles: “Proper STEM [science, technology, engineering and maths] stuff,” Glover says. At the end of the day, the children will have made 30 PE bibs, a useful resource for local schools where resources are increasingly stretched.
As well as training for children and adults, Makers HQ is a working sampling studio, which has produced lines of clothes for clients including an East London streetwear designer and a sportswear manufacturer working on swimwear for Muslim women.
The two-pronged business plan, training and sampling, was pressed into Glover’s hand when she was appointed studio manager in the summer of 2018. She was shown an office upstairs in the building, but asked to see others. When she saw the basement – a poorly lit room with blue carpets, she knew it was the place: “I saw these two units, they were grotty, with navy carpets, and I sat on a chucked out chair and I sat on a laptop and planned the kit I needed, how many machines I could fit in, wrote the job adverts.”
The room is now a fresh white, with knocked-through walls and state-of-the-art equipment. Glover knew she had found her first employee in Kim Watkins when Watkins cried during her interview. Watkins had run her own bridal shop in Halesowen in the midlands, making the dresses from scratch, until she moved back to Plymouth to be nearer to her family, who hail from Bude. She cried, she tells me later, “over the possibility that there was a job that I wanted to do”. “There was relief,” she says, “because doing what I do, the only time you can do it is usually by yourself.”
Glover says that one of the biggest barriers for the business is that consumers have got used to cheap, mass-produced goods. They are sometimes surprised by the cost of making clothes. “We’re not churning out stuff for Primark,” she says, placing her hand on a long stretch of floral fabric stretched out on the workbench. “We’re making dresses out of this fabric at around £50 per dress, to cut and sew it together. We’ve become a nation of consumers driven by price. We have to realise that actually, if you want quality, you have to pay for it.”
Makers HQ is already giving people out of work a fresh start in the textile industry. Howell says that before she went on the course she felt “really lost”. “I was crocheting one week and coming up with another hare-brained idea the next. On day two [of the course] I couldn’t even read a tape measure – the first pattern I did completely wrong because I was reading the tape measure wrong. But at the end of it, things just started falling into place.”
Before her interview, Howell watched a 15-minute documentary from 1984 about the old Jaeger factory on YouTube. “I walked past that building every day and never knew what it was,” she says. “It’s nice to be in a building with all that history, where beautiful clothes have been made. Hopefully it will grow and bring some of those skills back to Plymouth.”
Join our commenting forum
Join thought-provoking conversations, follow other Independent readers and see their replies
Comments