Technological leap for ‘urban mining’ could recover precious metals from electronic waste in seconds
Method could reduce demand for some conflict minerals and turn e-waste into ‘sustainable resource’
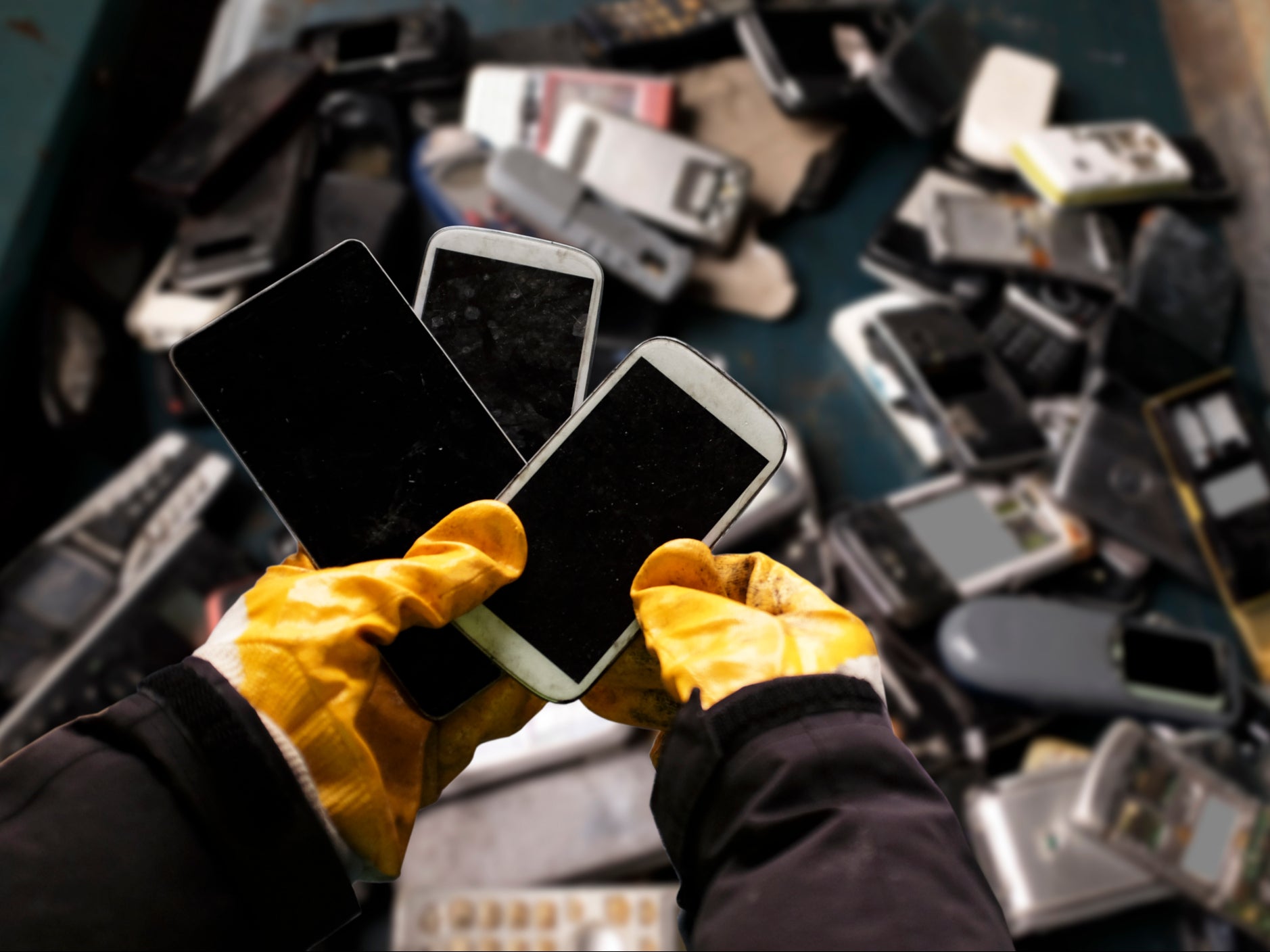
Your support helps us to tell the story
From reproductive rights to climate change to Big Tech, The Independent is on the ground when the story is developing. Whether it's investigating the financials of Elon Musk's pro-Trump PAC or producing our latest documentary, 'The A Word', which shines a light on the American women fighting for reproductive rights, we know how important it is to parse out the facts from the messaging.
At such a critical moment in US history, we need reporters on the ground. Your donation allows us to keep sending journalists to speak to both sides of the story.
The Independent is trusted by Americans across the entire political spectrum. And unlike many other quality news outlets, we choose not to lock Americans out of our reporting and analysis with paywalls. We believe quality journalism should be available to everyone, paid for by those who can afford it.
Your support makes all the difference.A new process to extract valuable metals from electronic waste could use 500 times less energy than existing methods, lower demand for mined raw materials, and produce eco-friendly waste, scientists have said.
The technique is based on the “flash Joule heating method”, which was pioneered to produce super-thin substance graphene from carbon sources such as wood and plastic.
But new adaptations by a team at Rice University in Texas mean the method can be used to recover substances including rhodium, palladium, gold and silver from waste so they can be reused.
It works by instantly heating the waste to 3,400 Kelvin (3,124C) with a jolt of electricity which vaporises the previous metals, and the gases are then vented away for separation, storage or disposal.
Residual highly toxic heavy metals such as chromium, arsenic, cadmium, mercury and lead are removed from the “flashed” materials, leaving a byproduct with minimal metal content, the team said.
With more than 40 million tons of e-waste produced globally every year, there is plenty of potential for this form of “urban mining”, which may also mean tech companies would not have to source all their raw materials from countries and regions with security, corruption and conflict issues.
“Here, the largest growing source of waste becomes a treasure,” said Rice University’s Professor James Tour.
“This will curtail the need to go all over the world to mine from ores in remote and dangerous places, stripping the Earth’s surface and using gobs of water resources.
“The treasure is in our dumpsters.”
He said an increasingly rapid turnover of personal devices such as the mobile telephone has driven the rapid rise of electronic waste around the world.
Currently only around 20 per cent of this waste is being recycled.
“We found a way to get the precious metals back and turn e-waste into a sustainable resource,” he said. “The toxic metals can be removed to spare the environment.”
The research team said they found flashing the e-waste requires some preparation.
Guided by lead author and Rice University postdoctoral research associate Dr Bing Deng, the researchers powdered circuit boards they used to test the process and introduced particular additives, like Teflon or table salt, and a dash of carbon black to improve the recovery yield.
Once flashed, the process relies on “evaporative separation” of the metal vapours.
The vapours are transported from the flash chamber under vacuum to another vessel where they condense into their constituent metals.
“The reclaimed metal mixtures in the trap can be further purified to individual metals by well-established refining methods,” Dr Deng said.
The researchers reported that one flash Joule reaction reduced the concentration of lead in the remaining char to below 0.05 parts per million, the level deemed safe for agricultural soils.
Levels of arsenic, mercury and chromium were all further reduced by increasing the number of flashes.
“Since each flash takes less than a second, this is easy to do,” Professor Tour said.
The Rice process consumes about 939 kilowatt-hours per ton of material processed – 80 times less energy than commercial smelting furnaces and 500 times less than laboratory tube furnaces, according to the researchers.
They said it also eliminates the lengthy purification required by smelting and leaching processes.
The research is published in the journal Nature Communications.
Join our commenting forum
Join thought-provoking conversations, follow other Independent readers and see their replies
Comments