Methane galore: Whisky and the green energy revolution
Whisky has a huge carbon footprint. But now a green energy revolution could be changing all that, says Jamie Merrill
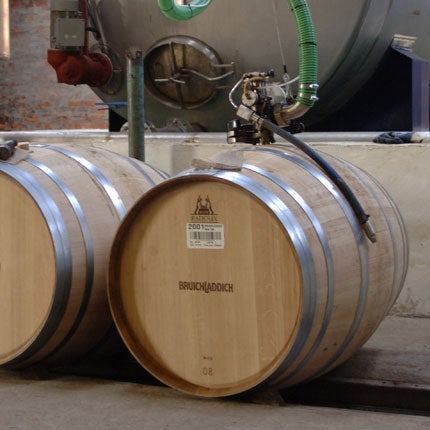
Your support helps us to tell the story
From reproductive rights to climate change to Big Tech, The Independent is on the ground when the story is developing. Whether it's investigating the financials of Elon Musk's pro-Trump PAC or producing our latest documentary, 'The A Word', which shines a light on the American women fighting for reproductive rights, we know how important it is to parse out the facts from the messaging.
At such a critical moment in US history, we need reporters on the ground. Your donation allows us to keep sending journalists to speak to both sides of the story.
The Independent is trusted by Americans across the entire political spectrum. And unlike many other quality news outlets, we choose not to lock Americans out of our reporting and analysis with paywalls. We believe quality journalism should be available to everyone, paid for by those who can afford it.
Your support makes all the difference.Facing Loch Indaal on the coast of Islay, the southernmost island of the Inner Hebrides, a small whisky distillery is one of the last places you might expect to find a revolutionary green energy project.
But Bruichladdich, a small privately owned distillery founded in 1881, is pioneering a system which is converting thousands of tons of yeasty waste into green energy.
Islay is home to some of Scotland's best-known whiskies, including Ardbeg and Lagavulin, and the industry has come under pressure to reduce its burgeoning carbon footprint, one of the highest of any food or drink. "Alcohol, like all food and drinks we consume, has a carbon footprint but until now we've tended to focus on high-profile examples such as green beans flown in from Kenya," says Tara Garnett, who runs the Food Climate Research Network at the University of Surrey. "But whisky, not only because we consume more of it, has a very large carbon footprint."
None of the main distilleries will release figures for their energy consumption but it's known that producing a bottle of beer – a far less energy-intensive process than whisky – creates up to 900g of carbon dioxide, compared to 21g for a cup of black tea. And whisky is often exported in heavy bottles with plenty of elaborate packaging.
Now though, thanks to consumer pressure and work by academics like Garnett, whisky distilleries are looking for greener production methods. Diageo, one of the biggest, has just invested £65m in green technology at its Cameronbridge distillery at Fife.
On Islay, Bruichladdich is leading the way with a pioneering process called anaerobic digester, which uses microbes to convert thousands of tons of pot ale (the yeasty by-product of producing 46,000 cases of single malt whisky a year) into methane gas, which is burned to make energy for the site.
Bacteria breaks down the organic waste in huge tanks without oxygen, meaning it cannot digest the waste fully, so, instead of just producing carbon dioxide, it produces methane, the main constituent of natural gas.
"Whisky has two main waste streams: the first is spent barley, which at Bruichladdich goes to feed local cattle; and pot ale – warm water and dead yeast – which until recently was trucked to the other side of the island and poured down a drain into the sea," says Mark Reynier, the company's owner. "The new equipment wasn't cheap. It cost us £275,000 to install but it's saving us £150,000 a year in electricity and the cost to truck our waste across the island for environmentally friendly disposal. Now our only real waste product is water."
The concept of anaerobic digestion isn't new. Irish scientist Robert Boyle first identified the concept around 1670 when he noted flammable gas bubbling to the surface of a muddy pond floor. Until recently, however, the technical expertise required, the enormous scale and low level of efficiency limited the process's commercial viability. But at Bruichladdich it has been made possible by a miniaturised digestion system.
The process began with 12 tons of bespoke microbes, bred to deal specifically with Bruichladdich's pot ale. These microbes were gradually fed into increasing volumes of pot ale in two vats to create biogas. As Reynier delicately puts it: "Our farting microbes are farting methane to power our generator which in turn feeds into the distillery's electrical distribution network."
Reynier, who now runs his Nissan Leaf electric car off the system, says the system provides 100 per cent of the distillery's power. He isn't a traditional environmentalist though: "I'm no eco-warrior. There are so many hare-brain environmental schemes out there and in the whisky industry that just don't work or are simply PR exercises. This, though, was a very interesting concept that made good business sense."
Join our commenting forum
Join thought-provoking conversations, follow other Independent readers and see their replies
Comments