How a PhD in technical textiles has proved really rewarding
Karthick Kanchi Govarthanam, 29, is in the final year of a PhD in technical textiles at the University of Bolton, where he’s been part of a team developing a flexible material that protects against knife slash wounds
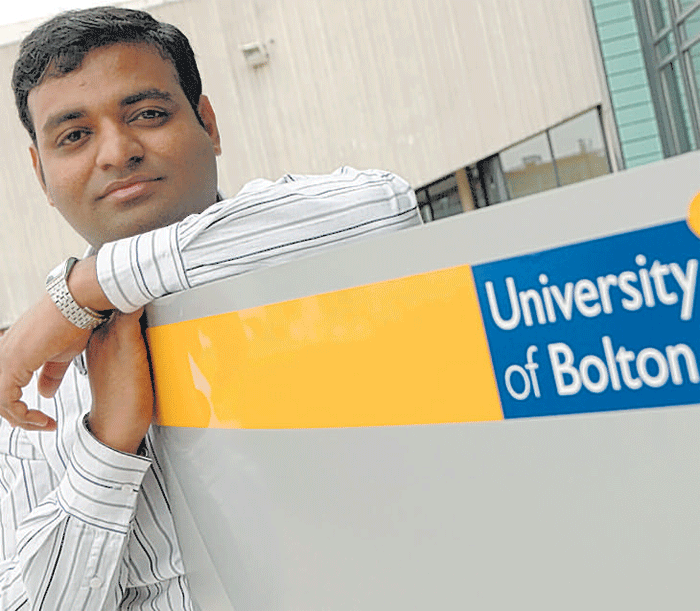
Your support helps us to tell the story
From reproductive rights to climate change to Big Tech, The Independent is on the ground when the story is developing. Whether it's investigating the financials of Elon Musk's pro-Trump PAC or producing our latest documentary, 'The A Word', which shines a light on the American women fighting for reproductive rights, we know how important it is to parse out the facts from the messaging.
At such a critical moment in US history, we need reporters on the ground. Your donation allows us to keep sending journalists to speak to both sides of the story.
The Independent is trusted by Americans across the entire political spectrum. And unlike many other quality news outlets, we choose not to lock Americans out of our reporting and analysis with paywalls. We believe quality journalism should be available to everyone, paid for by those who can afford it.
Your support makes all the difference.How did you come to do this PhD?
My first degree, in textiles technology, was at a university in southern India. In 2005, I came to England and did an MSc in advanced materials at Bolton, specialising in medical textiles, and geotextiles, which are the things used in roads and embankments. Then, in December 2007, I started this PhD.
What’s been your exact area |of research?
I’ve been working in a team producing material for a flexible protective garment, which will protect against slash wounds. The key element is the flexibility. Existing body armour-type garments are very heavy to wear, and offer no protection to areas like the neck, arms, legs and face. Our garment can be worn like a T-shirt or a balaclava, and the material we have designed is the first flexible material to pass the Home Office standard for slash resistance.
What stage is the research at?
The material has been patented and is being commercialised now. For the last two or three months, it has been manufactured by the industry partner who the university team have been working with.
What’s it made of?
The material is made from a number of components, including Kevlar, glass fibre and polyester. It makes the garments heavier than normal T-shirts, but much lighter that garments like leather jackets.
Are there any other uses?
Yes, the material can be used for garments to protect motorcyclists if they fall and are dragged along the road at high speed, and also to protect the forearms and stomachs of butchers using sharp knives. As the material has two layers, the outer layer can carry prints and designs, so civilian wear is also possible. In fact, we had civilians in mind when we first started developing this material.
How have you spent your time?
Most days I was working with the manufacturers, developing and testing the material, and at university back at the lab doing the work on a second property for the material, which gives it protection from bacteria, such as MRSA. The whole experience was really exciting. When you know you are doing something that is really needed and will help the community, it’s really rewarding.
How have you been funded? Because I’m an overseas student, I didn’t qualify for any Research Council funding, so I’ve been partly paying for this myself, but also receiving some funding from Future Textiles, the university’s industry partner on this project
What next?
I’m at the write-up stage at the moment, but I’ll be working on this project with the university and industry for the next six months. In the future, I want to continue to be involved in developing new products.
Join our commenting forum
Join thought-provoking conversations, follow other Independent readers and see their replies
Comments