Nasa successfully tests first ever 3D-printed rocket component
Additive printing could lead to cheaper and quicker production of rockets
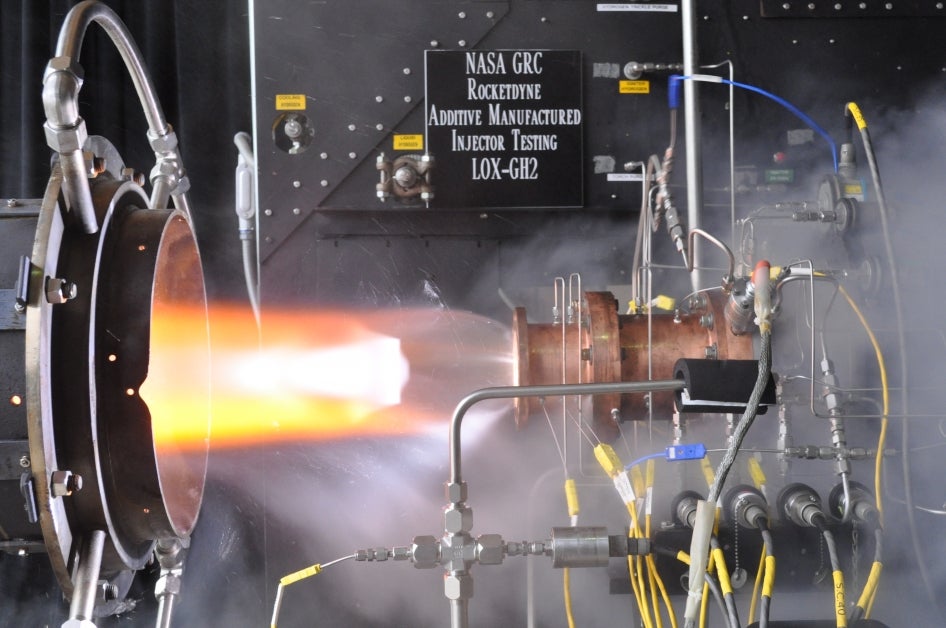
Your support helps us to tell the story
From reproductive rights to climate change to Big Tech, The Independent is on the ground when the story is developing. Whether it's investigating the financials of Elon Musk's pro-Trump PAC or producing our latest documentary, 'The A Word', which shines a light on the American women fighting for reproductive rights, we know how important it is to parse out the facts from the messaging.
At such a critical moment in US history, we need reporters on the ground. Your donation allows us to keep sending journalists to speak to both sides of the story.
The Independent is trusted by Americans across the entire political spectrum. And unlike many other quality news outlets, we choose not to lock Americans out of our reporting and analysis with paywalls. We believe quality journalism should be available to everyone, paid for by those who can afford it.
Your support makes all the difference.Nasa has successfully tested the first-ever 3D printed rocket component. “This space technology demonstration may lead to more efficient manufacturing of rocket engines,” said NASA in an official statement, “saving American companies time and money.”
The component in question – a fuel injector described as “the heart of a rocket engine” - was subjected to a serious of firing tests using liquid oxygen and gaseous hydrogen. The injector was created by the company Aerojet Rocketdyne by a method using high-powered lasers to melt and fuse metallic powders into the desired shapes.
"NASA recognizes that on Earth and potentially in space, additive manufacturing can be game-changing for new mission opportunities, significantly reducing production time and cost by 'printing' tools, engine parts or even entire spacecraft," said Michael Gazarik, Nasa's associate administrator for space technology in Washington.
"3-D manufacturing offers opportunities to optimize the fit, form and delivery systems of materials that will enable our space missions while directly benefiting American businesses here on Earth."
The component successfully tested was built in less than four months, whilst traditional methods would have taken more than a year, giving a 70 per cent reduction in costs.
"Rocket engine components are complex machined pieces that require significant labor and time to produce. The injector is one of the most expensive components of an engine," said Tyler Hickman, an engineer responsible for testing the injector.
After this successful experiment the injector’s creators now say they will be ready to move on to “demonstrate the feasibility of developing full-size, additively manufactured parts.”
Join our commenting forum
Join thought-provoking conversations, follow other Independent readers and see their replies
Comments